Introduction
Today’s rapidly evolving world has seen many industries power major hardware innovations. Electrification, renewable energy, and last-mile delivery require cutting-edge hardware products. Many of these companies are adopting industry 4.0 software, a product traceability system has become a mainstay in recent years. The ability to trace any production issue back to a specific batch of parts is now required for manufacturers to remain competitive. This article will explore the benefits of traceability data tools.
Definition of Traceability
Traceability is the ability to track the journey of parts through the manufacturing process, from raw materials to finished goods. The breadth and depth of data collection depend on the industry and the value of the part produced. For example, the automotive and aerospace sectors have used traceability systems for decades, often tracing hundreds of components per finished part, while the consumer packaged goods industry typically traces batches of raw materials used in their products. Specific types of data vary but often include:
- Part numbers for all critical components
- Supplier details & incoming quality reports
- Sub-assembly serial numbers or lot codes
- Quality control checks
- Shipping details between supply chain nodes
Benefits of Traceability
A robust traceability system provides many business benefits. It improves cross-functional communication and builds a system of record for operations, engineering, and customer support teams. Possible benefits include:
- Quality control
- Compliance with regulations & standards
- Supply chain visibility
- Recall management
- Warranty and service management
- Supplier accountability
- Continuous improvement
- Brand protection
Improved Quality Control
Traceability improves quality control by providing built-in statistical process control for numerical data—production traceability tracks which specific parts are assembled, by who, and at what time. For example, a drone manufacturer notices their motors are suddenly burning out within a few weeks of operation, causing a production line down situation. Using Serial, a quality engineer can quickly look up all of the details for the motor. They can then check all drones built within the last few weeks and filter by their motor supplier. All of the failing parts are from the same batch and supplier. They can quarantine these parts and use their secondary supplier to unblock production.
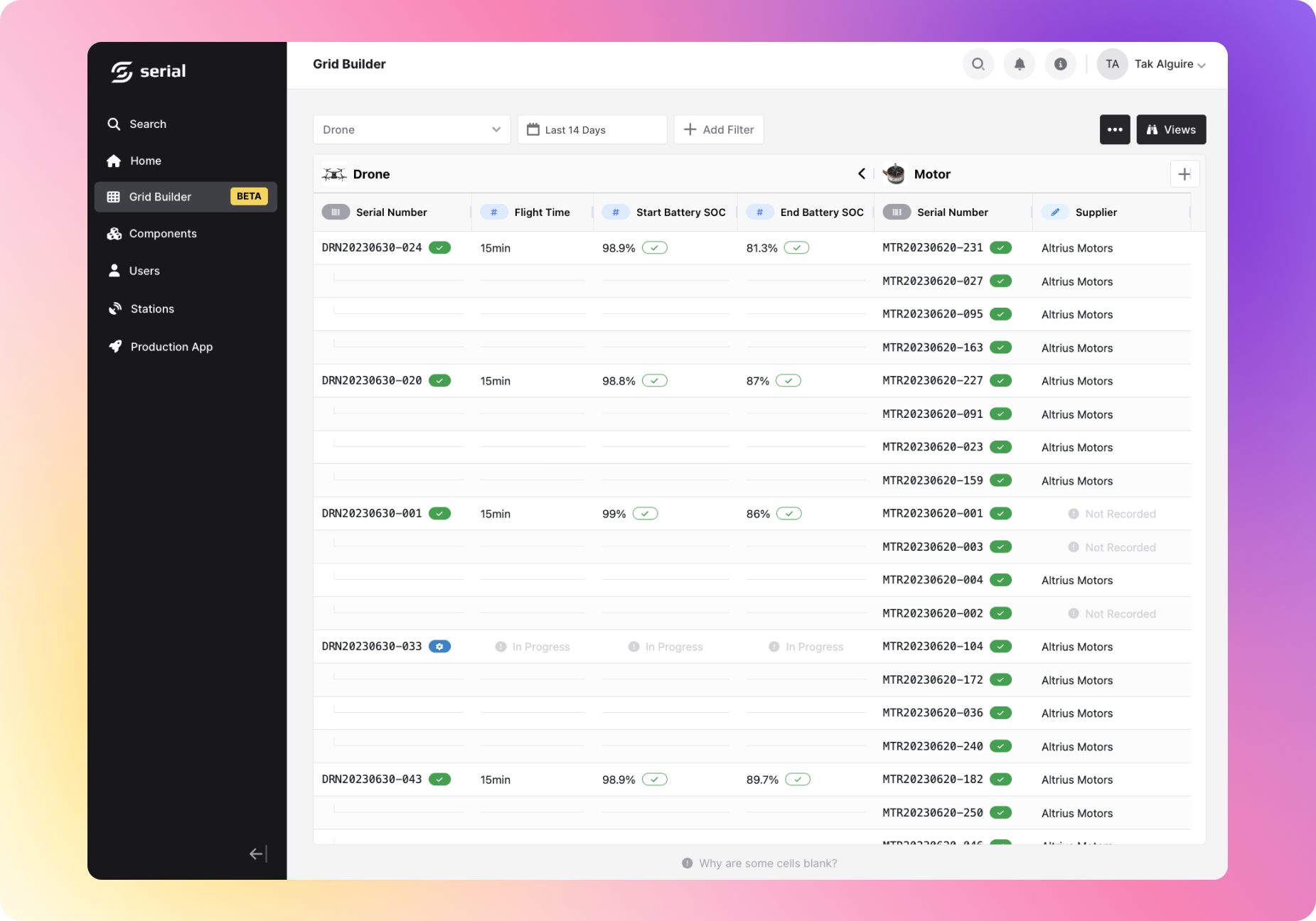
Compliance with Regulations & Standards
Traceability can help companies to comply with a variety of different regulatory requirements. Tracking the processes, materials, and products to ensure consistent quality and facility corrective actions is critical. Here are a few major standards:
ISO 9001 - Quality management systems Widely adopted standard in automotive, aerospace, electronics & consumer goods manufacturing. A broad standard to help companies organize their systems and manage supply chains effectively.
ISO 13485 - Medical devices - Quality management systems Specifically used in the medical industry to ensure safety, reliability, and regulatory compliance of medical device manufacturing. A comprehensive standard covering product lifecycle, design, development, production, installation, and servicing.
International Traffic in Arms Regulations (ITAR) is a US regulation that controls the export and import of defense-related articles and services. It aims to safeguard national security by regulating the transfer of sensitive military technologies to foreign entities or individuals.
Supply Chain Visibility
Supply chain traceability is vital to track material flow between and within supply nodes. Serial numbers or lot tracking can be used depending on the importance of the part. Our drone company tracks their high-value parts by serial number and other parts like propellers by lot code. In the manufacturing phase, they can see the macro movement of parts between supply nodes or dive deep into the micro movement of parts through specific assembly steps. From the design perspective, they can quickly discover which suppliers of particular parts are correlating to higher yields or better product life and optimize their supply volumes accordingly.
Recall Management
When a company has identified a critical quality concern that impacts the primary function of its product, it will issue a recall to correct it. The Automotive industry frequently issues recalls to correct problems. Here is an actual recall from Ford:
NHTSA Recall Number: 23V-070
Date Issued: April 25, 2023,
Total Vehicles: 944
Estimated percentage with a defect: 3% (~28 vehicles)
Affected Vehicles: 2022-2023 Ford F-150, Explorer, Bronco
Defect Summary: A loose (extra) bolt may be present in the automatic transmission of affected vehicles. This could prevent the transmission from engaging the park gear.
This is an example of traceability at work. The defect impacts over 6 model years. However, only 944 specific vehicles were issued a recall inspection. One could hypothesize that the same assembly technician worked on all affected vehicles. Ford found this trend and only recalled the vehicles touched by this technician. Thus preventing the costly recall of checking all vehicles in the 6 model year window.
Warranty and Service Management
Many manufacturers offer comprehensive warranties or service plans. Traceability helps companies track the initiation and completion of their offered warranty plans. For example, anyone can check their iPhone warranty on Apple’s website using the serial number.
Supplier Accountability
Traceability software can help hold suppliers accountable for their quality requirements. All quality reports or compliance documentation can be associated with the incoming serial number or lot code. The benefits of tracking these details include the following:
- Track supplier performance - product quality, on-time delivery, responsiveness, etc.
- Root cause analysis - trace quality issue back to a specific supplier
- Collaboration & communication - a centralized platform for data sharing
Continuous Improvement
Effective traceability systems help engineering teams to optimize their manufacturing processes. For example, our drone company is experiencing a 90% yield for one of its functional tests. Their team analyzed all the parts through this functional test in the past two months and ran an automated commonality analysis. They discovered that the same technician assembled over half of the failing parts. This particular technician was routing the wire harness slightly differently, as the work instructions were unclear. Resolving variance resulted in a 3% yield increase. Leveraging automated commonality analysis helps engineering teams focus their efforts on signals instead of searching in the dark.
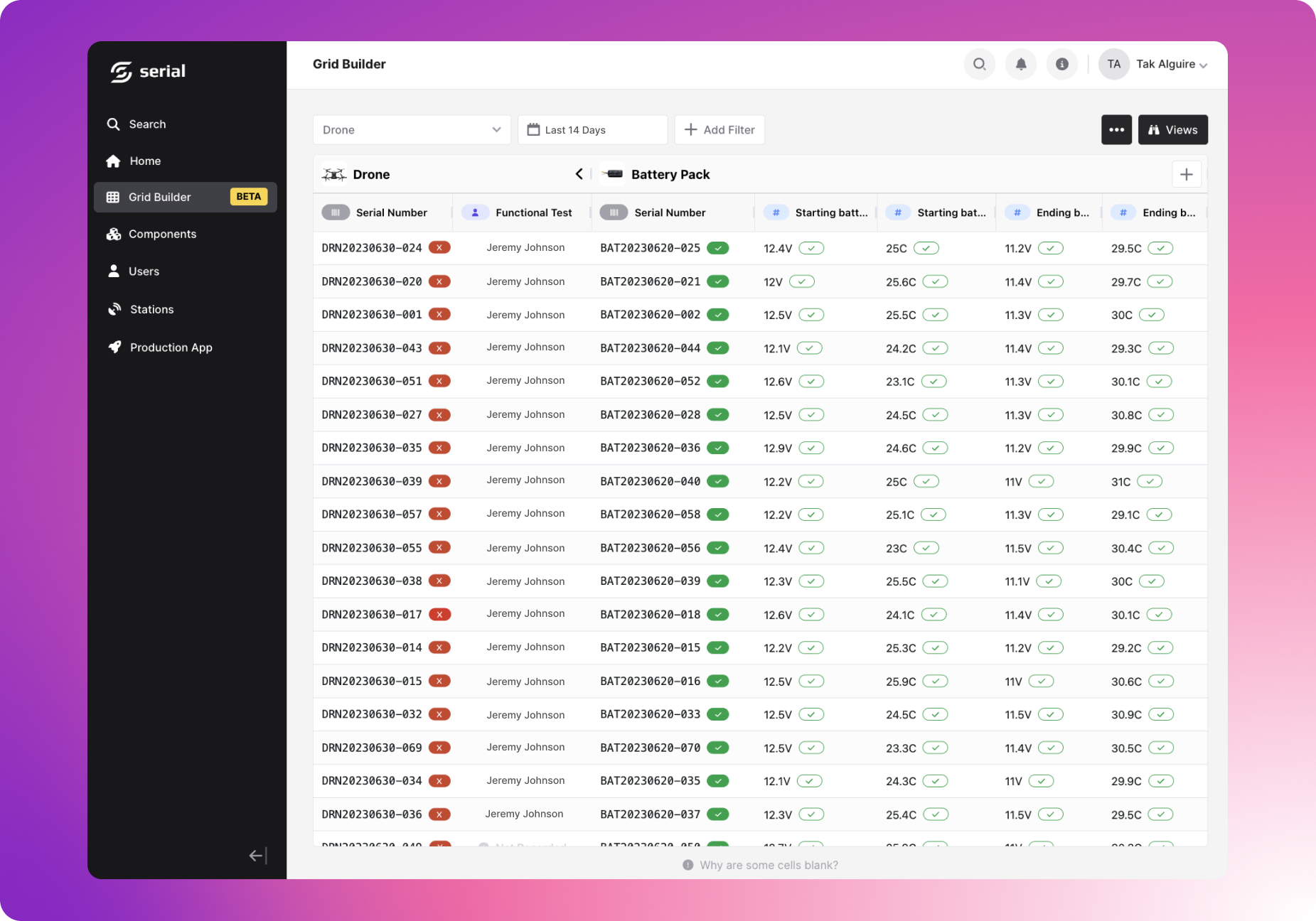
Brand Protection
The pandemic created global supply shortages across a variety of industries. The semiconductor shortage was one of the most publicized due to its massive impact on dozens of sectors. Counterfeit semiconductors became a real problem as companies bought any supply they could find. Traceability tools enabled companies to ensure the authenticity of their product.
Challenges of Traceability Systems
Traceability software does not come without its drawbacks. The infrastructure to enable traceability can be complex and costly. Additionally, there are security concerns as this is business-critical data.
Cost of Implementation
Companies have two choices for implementing a traceability system. Hire engineers and build the systems in-house, or purchase off-the-shelf software. Both have their pros and cons. Building in-house is costly as it will require dedicated software developers and IT resources to manage hosting, distribution, and security. While purchasing off-the-shelf software is often a higher cost in year 1, companies can avoid the long-term challenges of building an entire tool from scratch.
There are also per-part costs to add serial numbers or barcodes. Typically results in only high-value parts being serialized, while low-value parts are batch controlled.
Technical Limitations
Technical challenges also boil down to the in-house vs. off-shelf choice. In-house teams must consider system architecture, performance optimization, and complex feature roadmaps. This challenge becomes significantly prominent for the off-the-shelf route.
There can be technical limitations to tracking specific production processes as parts are not or cannot be serialized due to material concerns or lack of space for a readable barcode.
Security Concerns
Creating a robust traceability system also creates an increased risk of brand damage if the data falls into the hands of a malicious user. There are many options to ensure data security, such as:
- On-premise deployments - air-gapped data storage
- AWS gov cloud
- Cloud hosting
There is no golden ticket when it comes to data security. Every option has pros and cons. For example, moving to on-premise deployments requires hardware and network infrastructure to be installed onsite. This could take months to organize and set up, while cloud deployments can be initiated in a matter of hours.
Final Thoughts
In conclusion, traceability is critical in modern manufacturing operations. It enables tracking parts from raw material through to finished goods, improving operations from quality control to brand protection. Drawbacks are primarily implementation costs and technical limitations. Companies should consider the in-house vs. off-shelf tradeoffs. Companies must invest in robust traceability systems to remain competitive and meet the demands of the evolving manufacturing landscape.