Introduction
A manufacturing execution system (MES) is as essential to a factory as an operating system (OS) is to a computer. An operating system schedules tasks, allocates resources, and monitors performance to harmonize the computer's operation. Similarly, an MES is responsible for production planning, assigning work to production lines, and monitoring the performance of the factory. Both systems must balance a delicate house of cards; too many mistakes and it all comes crashing down.
Definition of an MES
MES software integrates directly with manufacturing operations to track, control and document the assembly of parts into finished goods. MESs typically integrate to business-system counterparts like ERPs and PLMs, while also integrating directly with hardware in a factory. Thus most MES solutions are highly customized to their businesses.
Top 3 Benefits of an MES
A well-integrated MES provides three main benefits to any company's manufacturing operations' bottom line.
- Increased Efficiency
- Realtime Visibility
- Quality Control
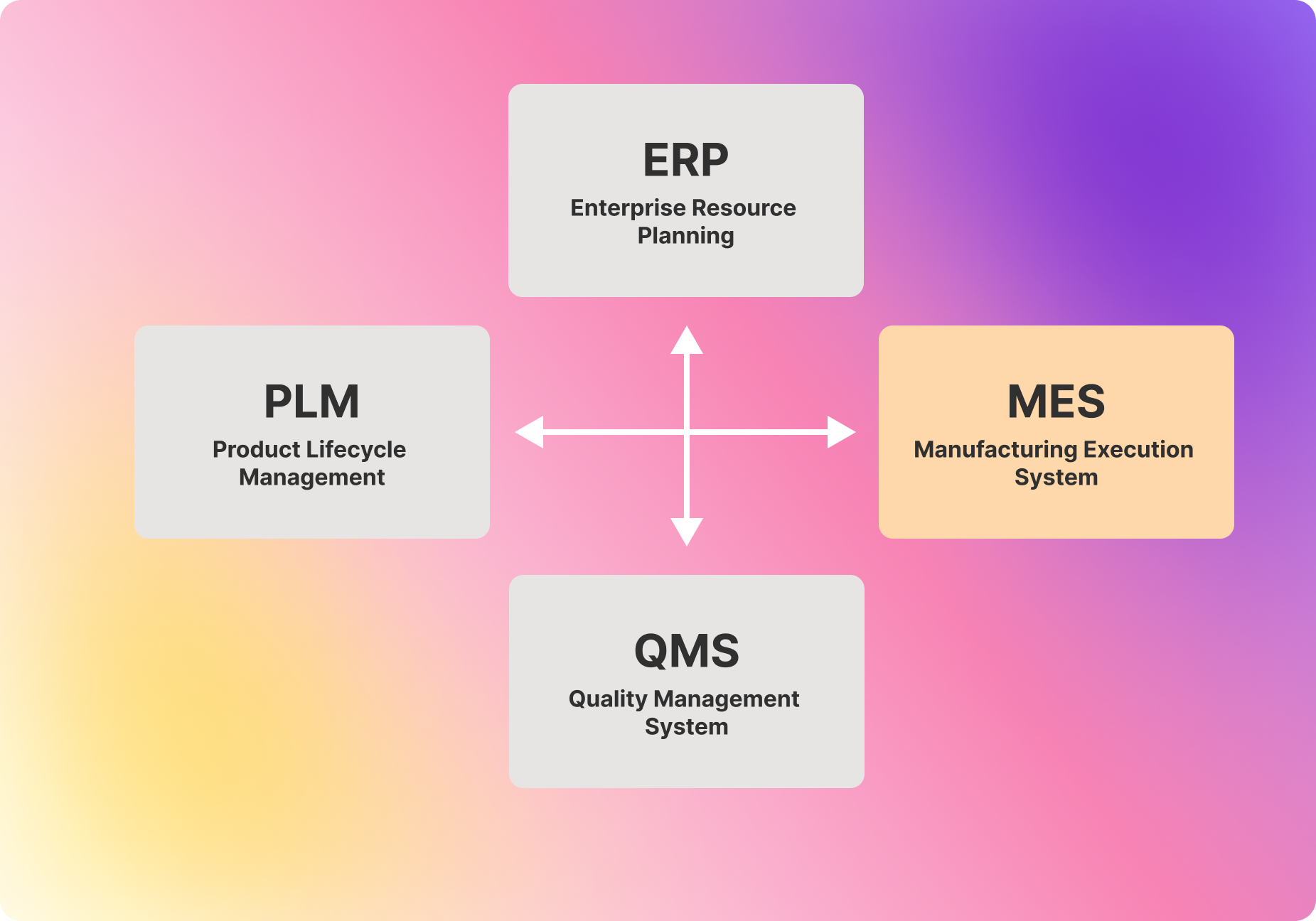
Benefits of Increased Efficiency
The bread and butter of an MES is to increase the efficiency of a factory by outputting more finished goods. Modern operating systems prioritize and parallelize tasks to optimize performance. They also dynamically adjust CPU and memory resources for particular applications to ensure stability. Similarly, MESs prioritize schedules based on cycle times and dynamically reassign equipment or labor resources to fill shortages or handle planned downtime.
Work Scheduling
One of the core features of an MES solution is to generate manufacturing schedules to determine which lines produce which parts, using the cycle time of a given process and the available inventory. The MES must also consider the stock of various sub-assembles to ensure smooth continuous production. Legacy MES tools often integrate into inventory management systems and require manual entry of cycle time. This reliance on manual information severely inhibits the realtime capability of an MES to handle changes in the production schedule.
Resource Optimization
Advanced MES solutions will optimize labor and equipment to reduce waste. Companies in different industries will realize this differently, but here are some standard MES optimizations.
Labor Allocation
It increases labor utilization by shifting labor to tasks based on material shortages or plant floor inefficiencies. Some MESs can identify more efficient operators for specific tasks and optimize schedules to take advantage.
Line Balancing
It identifies bottlenecks and shifts the output of particular machines or lines to minimize the impact of a material shortage.
Energy Optimization
With the advent of lights-out manufacturing, some manufacturing processes like CNC milling or laser cutting can now be run when energy is more affordable, thus introducing marginal cost savings on variable electricity costs.
Machine Maintenance
An MES can optimize the maintenance schedule or even pre-empt a maintenance event by monitoring the performance of particular machines. All while ensuring minimum downtime and impact on production.
Paperless Workflow
Paper travelers are common in manufacturing to track the assembly progress or quality check results. An MES eliminates the need for travelers as all of the content is now electronically tracked; this has a two-fold advantage as data collection is now traceable and searchable. Some MES tools offer digital work instructions, eliminating the need for paper at most production steps.
Benefits of Realtime Visibility
Realtime visibility into manufacturing operations is crucial to minimizing waste and downtime. Computer operating systems give users realtime insights into CPU and memory utilization, network stability, and even performance logs. Moreover, MES solutions can provide engineers with realtime equipment utilization and live yields.
Immediate Decision-Making
Realtime insights into machine malfunctions or product yields allow production supervisors to address issues immediately, minimizing production downtime. Engineering teams can also use this to root cause quality problems in a fraction of the time it would take using conventional means.
Supply Chain Integration
Realtime product yields and inventory levels close the feedback loop for supply chain teams, so they can always be prepared and know when to reorder parts or expedite existing shipments.
Benefits of Quality Control
Computer operating systems provide a consistent hardware-agnostic foundation for application developers, minimizing hardware-related crashes and ensuring a baseline for performance. Similarly, MES software tracks all assembly steps to transform a product from parts to finished goods, inherently introducing traceability to a manufacturing environment. Data previously tracked in Excel is now automatically recorded.
Workflow Interlocks
All parts will have prescribed assembly steps. For example, when manufacturing a drone, the motors and flight computers must undergo a calibration step before a flight test can be performed. If a drone skips the calibration step, the MES can reject the flight test and prevent this drone from continuing production, ensuring consistency in manufacturing, which is essential to ensure quality.
Reduced Non-Conformance Costs
Continuing the drone example, let's say another drone fails the flight computer calibration step. The MES will label this defect (non-conformity), which will:
A. Stop the drone from continuing production
B. Initiate a rework loop
Some MES solutions can label specific failures to handle different rework workflows. For example, was it a sensor failure or a power failure? The line between an MES and QMS starts to muddle here. Depending on the complexity of the product, a QMS might be required. Non-conformity tracking enables companies to rework more parts and improve their processes to reduce scrap costs.
Conclusion
Providing a perfect blend of process optimization, automation, and business-system integration, an MES is vital in any manufacturing enterprise seeking to enhance its performance. Whether organizing the chaos of a factory or a computer system, the principles of efficiency, visibility, and quality reign supreme.